Prevent unplanned downtime with new and replacement gearboxes from Philadelphia Gear®. When your equipment needs to catch up with manufacturing needs, process improvements, or technological advances, we provide the cutting-edge processes and facilities to keep your operations reliably moving.
Backed by over 130 years of design engineering and manufacturing expertise, Philadelphia Gear offers an array of flexible gearbox configurations to fit your specific footprint. We can create nearly any industrial gear arrangement, including parallel shaft, double helical, planetary / epicyclic, bevel helical, and more – there is virtually no gear-related challenge we haven’t seen and solved before.
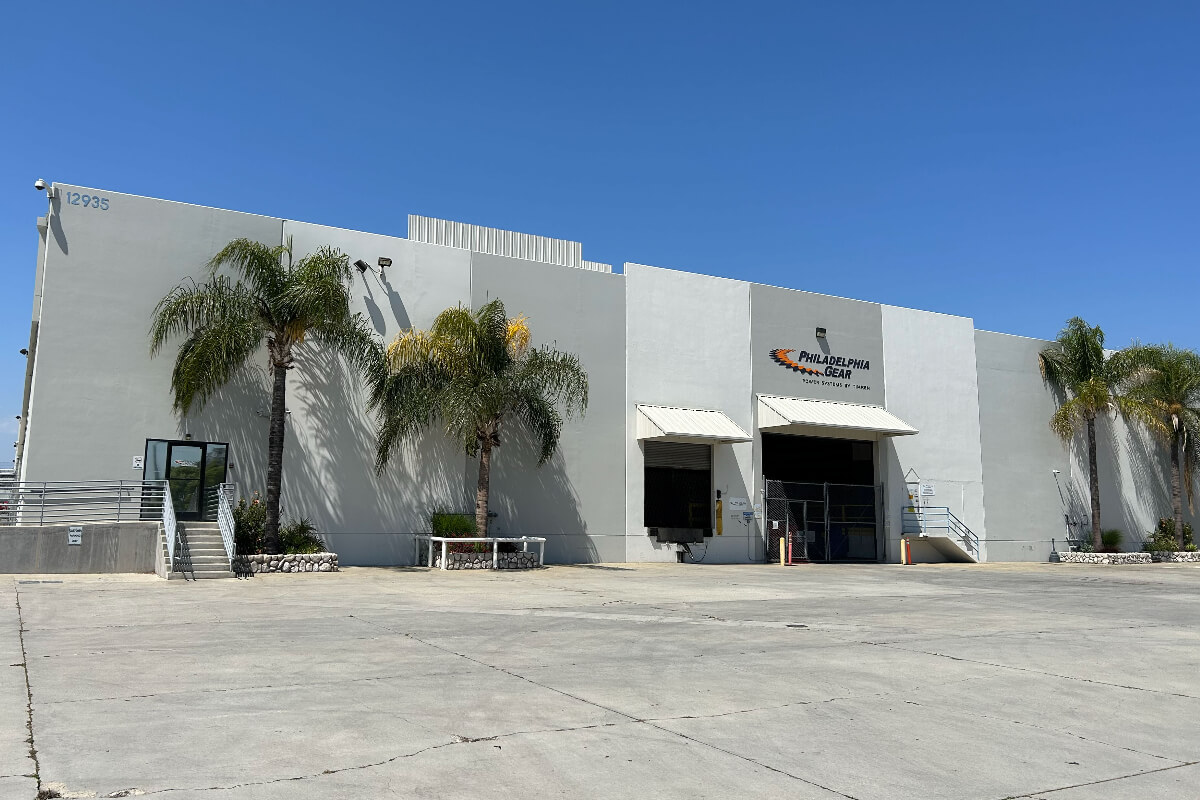
NEARLY 1,000,000 SQUARE FEET OF MANUFACTURING EXCELLENCE
Access expert support near you: Our regional service and manufacturing centers are strategically located near the industries they serve. In addition to their own engineering and manufacturing capabilities, each facility is backed by our central technical and engineering hub in King of Prussia, Pennsylvania.
Unique to the gear industry, each location also has immediate access to our vast digital library, including four million pages of drawings, bills of materials, and other engineering documents — spanning over 130 years of technical information for Philadelphia Gear, Western Gear, WesTech Gear, De Laval Steam Turbine, Hamilton Gear, and GE marine gear.
Learn more about our speed and power ranges by application type:
SPEED AND POWER RANGES BY APPLICATION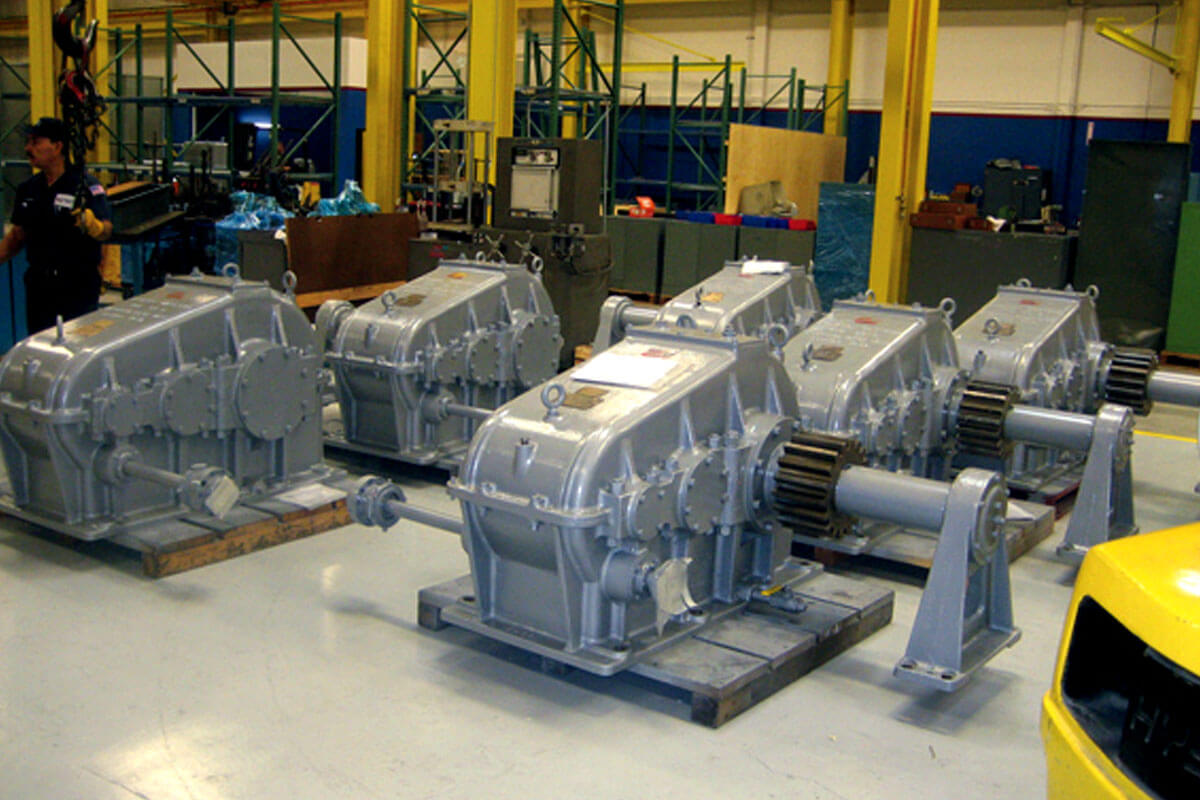
STATE-OF-THE-ART EQUIPMENT TO SOLVE COMPLEX PROBLEMS
Philadelphia Gear invests in cutting-edge manufacturing, checking, and testing equipment to ensure our gearboxes keep up with your most demanding applications.
- 70-ton lifting capacity
- Certified welders and non-destructive testing
- EPA-approved painting and cleaning facilities with wastewater recovery system
- Plant flows maximized to increase production efficiency and throughput
- Ergonomically designed work cells
- Bearing induction heaters to 10”
- Gear cable induction heating system to any size
- All sites independently ISO-certified
- Magnetic Particle Inspections (MPI) after case hardening and grinding
- Laser alignment on all test stands
- Faro arms for housing and component inspections
- Various test stands capable of achieving full load simulations to 60,000 HP
- Compliant with API testing standards as required
- 2500 HP cooling towers
- Horizontal boring mill tables up to 98” L x 48” W
- Vertical turning lathes to 42” D
- 300-ton press
- Key seating to 1.5” W x 15” L
- Shaft turning to 40” D x 16’ L
- I.D. grinding to 22” D
- O.D. grinding to 40” D x 100” L
- Turning shafts to 56” D x 120” L
- Jig mill capabilities for housings and components
- Surface grinding to 42” D
- 8’ arm drill press
- Form grinding up to 4 meters
- Gear checking to 4 meters
- Horizontal and vertical 5-axis machining centers
- AGMA quality ratings of 8-15, depending on the application
- CNC gear hobbing to 1.8 meters
- Gear shaving to 90”
- Multiple roll stands to check gear contacts up to 100” center distances, and to simulate housing parallelism
- Gear balancing to 30,000 lbs.
- Gear shaping to 36”
- Isolated assembly areas