WE SERVICE & REPAIR EVERY GEARBOX BRAND
- Allen Gear
- Amarillo
- BHS-Voith
- Black Clawson
- Brad Foote
- David Brown
- John Brown
- Chemineer
- Cleveland
- Delaval Steam Turbine*
- D.O. James
- Elliott
- Falk
- Farrell
- Flender
- Flender-Graffenstaden
- Foote Jones
- General Electric
- Hamilton Gear*
- Hansen
- Hitachi
- Horsburgh & Scott
- Lightnin
- Link-Belt
- Lufkin
- Maag
- Marley
- Mitsubishi
- Nuttal
- Philadelphia Gear*
- Philadelphia Mixers
- Renk
- Siemens
- Standard Machine*
- Sumitomo
- Thyssen
- WesTech*
- Western Gear*
- Westinghouse
*Philadelphia Gear, WesTech, Western Gear, Delaval Steam Turbine, Standard Machine, and Hamilton Gear are all registered trademarks of The Timken Company or its affiliates.
MINIMIZE DOWNTIME WITH EMERGENCY OVERHAUL SERVICESAt Philadelphia Gear, we understand how critical an equipment failure can be for your business. That’s why our service team is available 24/7 to help keep your operations running at peak efficiency.
How it works
-
1
Reach out
-
2
Initial Inspection
-
3
Disassembly and cleaning
-
4
Assembly and testing
-
5
Painting, preserving, and shipment
-
6
Rest easy
1 Reach out
With 24/7 gearbox and gear repair service capabilities, our team is standing by and ready to help with your toughest gearbox challenges. Contact our team today with photos of your set to get the process started.
2 Initial Inspection
Onsite or in our facilities, our expert team of specialists will inspect your unit to determine the root cause of the failure. After our teams inspection is over, we’ll provide a detailed report with images.
3 Disassembly and cleaning
Our team takes apart and cleans the unit, and schedules manufacturing for replacement parts. For uprating, we’ll make necessary changes and incorporate them into the manufacturing process.
4 Assembly and testing
Once the components are complete, we reassemble and rigorously test the gearbox, measuring endplay, tooth contact and backlash, temperature, sound, vibration levels, and more.
5 Painting, preserving, and shipment
After the gearbox is reassembled and thoroughly tested, we epoxy paint and preserve the unit for storage. Once dried and preserved, we will send your gearbox along to you with documentation to keep it running smoothly for years to come.
6 Rest easy
All overhauls performed at our service and manufacturing centers are backed by a best-in-industry three-year warranty. Should any issues arise with your equipment, reach out to our expert gearbox repair team to get back up and running quickly.
Testing the gearbox after repairs is crucial to ensure that the components have been properly restored and are functioning optimally. It helps identify any lingering issues, guarantees the gearbox’s reliability, and ensures its safe and efficient operation in real-world conditions.
At Philadelphia Gear, we understand how critical an equipment failure can be for your business. That’s why our service team is available 24/7 to help keep your operations running at peak efficiency.
How it works
-
1Reach out
-
2Initial Inspection
-
3Disassembly and cleaning
-
4Assembly and testing
-
5Painting, preserving, and shipment
-
6Rest easy
1 Reach out
With 24/7 gearbox and gear repair service capabilities, our team is standing by and ready to help with your toughest gearbox challenges. Contact our team today with photos of your set to get the process started.
2 Initial Inspection
Onsite or in our facilities, our expert team of specialists will inspect your unit to determine the root cause of the failure. After our teams inspection is over, we’ll provide a detailed report with images.
3 Disassembly and cleaning
Our team takes apart and cleans the unit, and schedules manufacturing for replacement parts. For uprating, we’ll make necessary changes and incorporate them into the manufacturing process.
4 Assembly and testing
Once the components are complete, we reassemble and rigorously test the gearbox, measuring endplay, tooth contact and backlash, temperature, sound, vibration levels, and more.
5 Painting, preserving, and shipment
After the gearbox is reassembled and thoroughly tested, we epoxy paint and preserve the unit for storage. Once dried and preserved, we will send your gearbox along to you with documentation to keep it running smoothly for years to come.
6 Rest easy
All overhauls performed at our service and manufacturing centers are backed by a best-in-industry three-year warranty. Should any issues arise with your equipment, reach out to our expert gearbox repair team to get back up and running quickly.
Testing the gearbox after repairs is crucial to ensure that the components have been properly restored and are functioning optimally. It helps identify any lingering issues, guarantees the gearbox’s reliability, and ensures its safe and efficient operation in real-world conditions.
EXTEND THE LIFE OF YOUR EQUIPMENT WITH GEARBOX UPGRADES
Gain greater confidence in your gears with our full selection of upgrade services.
Gearing upgrades
|
Lubrication upgrades
|
Bearing upgrades
|
Smart add-ons
|
WE WORK HARDER TO DO IT RIGHT.
Unlike other gearbox companies, we don’t cut corners with a cookie-cutter approach. Instead, we reverse engineer every gearbox or component to exact OEM standards, taking your specific needs into account.
Our experts are trained in gearbox failure root cause analysis. We take the time to provide full disassembly and cleaning, inspection and measurement, engineering evaluation and recommendations, and gearbox repair and spin testing.
That’s why Philadelphia Gear is your first choice for long-term reliability — for products from Philadelphia Gear and any other brand.
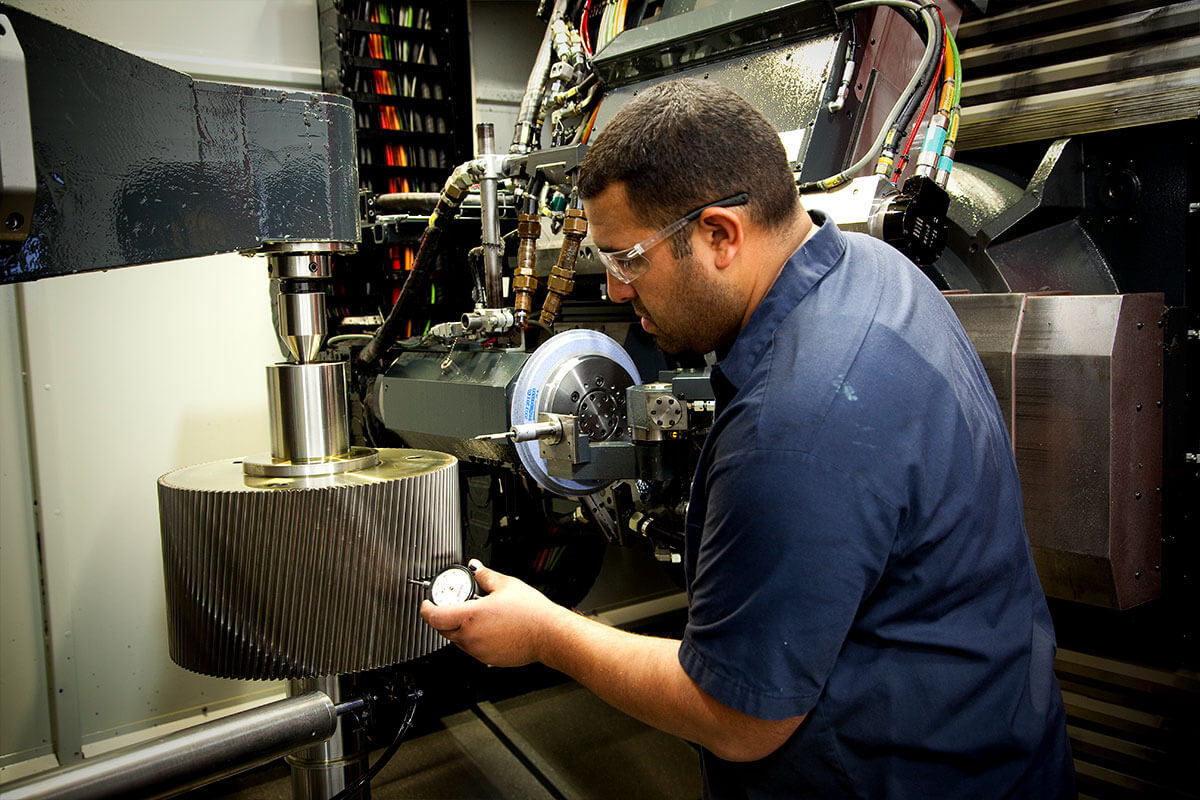
DON’T PUT YOUR OPERATIONS AT UNNECESSARY RISK. CONTACT PHILADELPHIA GEAR TODAY.Our service team is standing by to help with your gearbox maintenance and repair needs.
Call 800-766-5120 to get started or contact your regional representative directly by clicking the link below.
Find your regional service center
Our service team is standing by to help with your gearbox maintenance and repair needs.
Call 800-766-5120 to get started or contact your regional representative directly by clicking the link below.
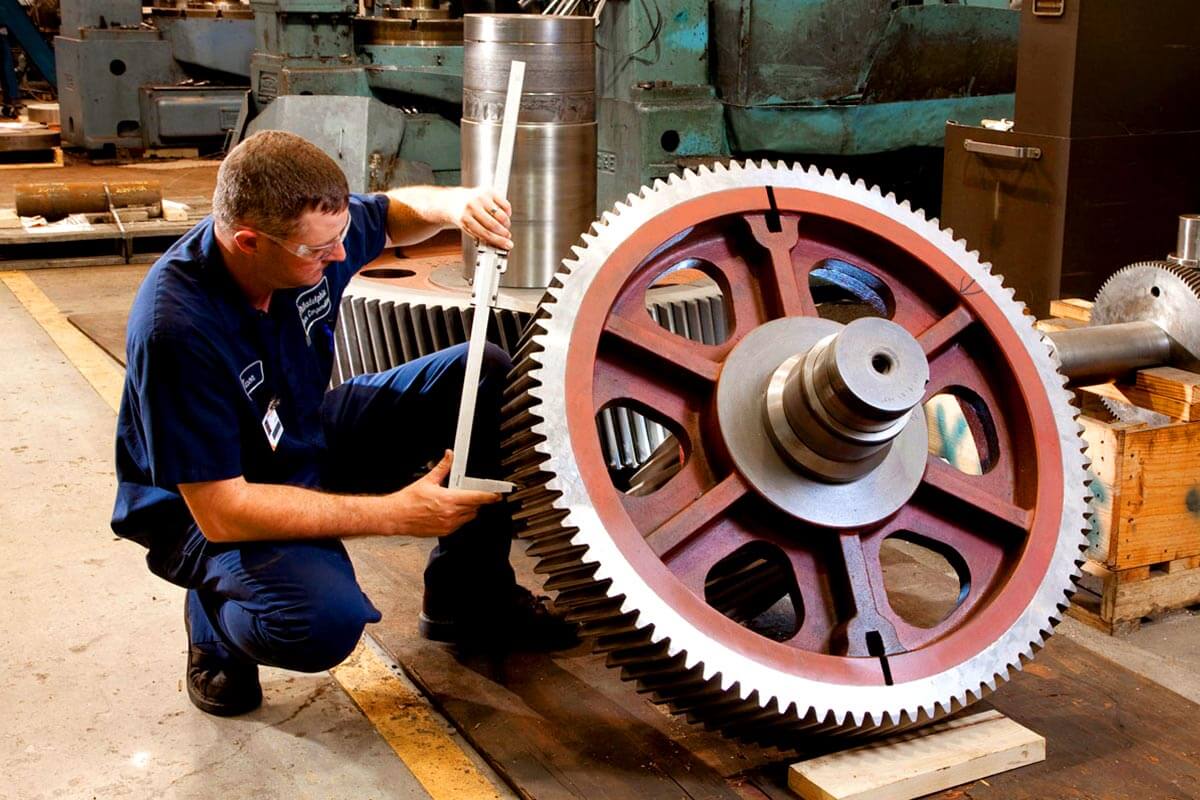