Case Study
Philadelphia-brand gear drive designs help protect Texas Gulf Coast from hurricane flooding
In September 2019, residents in Surfside Beach, Texas, and surrounding areas prepared for a state of emergency as Hurricane Dorian approached. While the storm didn’t turn out to be as severe for the region as Hurricanes Rita and Katrina were in 2005, the Velasco Drainage District stood ready to manage any resulting storm water.
First established in 1908 to manage storm surges and flooding, Velasco maintains 50 miles of levees. It operates 14 pump stations that cover 236 square miles of the Texas Gulf Coast. The pump network has the capacity to pump 4,770,000 gallons a minute – the equivalent of filling 8.7 regulation Olympic-sized swimming pools in just 60 seconds.
The Primary Challenge
Philadelphia Gear, now part of Timken Power Systems, outfits all but one of Velasco’s pump stations with reliable, high-performing gearboxes and provides ongoing service. Velasco recently called in Philadelphia Gear to solve oil pressure problems with a gearbox in operation since 1978 at its Ditch #13 station.
“Pump stations only run when it’s raining and stormwater drainage is required,” says Dennis Howard, territory manager for Philadelphia Gear. “Although they get infrequent use, it’s critical that they function properly during hurricane season and any time there is heavy rainfall.”
To ensure everything remains in working order, Velasco routinely runs each pump on a regular schedule. They began to have problems maintaining oil pressure during the shutdown cycle, which reduces the engine to an idle RPM for the cool-down period. The shaft-driven oil pump would not supply the minimum oil pressure required, resulting in an engine shutdown by the pressure switch before the cool-down cycle.
When Howard inspected the unit, he discovered that the original gearbox was supplied with an electric/air cooler, but the gearbox lube system was using the engine cooler located at the end of the engine opposite of where the gearbox was situated. The changes altered the discharge piping size and created an excessive distance for the oil to travel through the system. In addition, debris had blocked a spray nozzle and the combination of both issues caused the gears to develop pitting, which could have eventually led to catastrophic gear tooth failure.
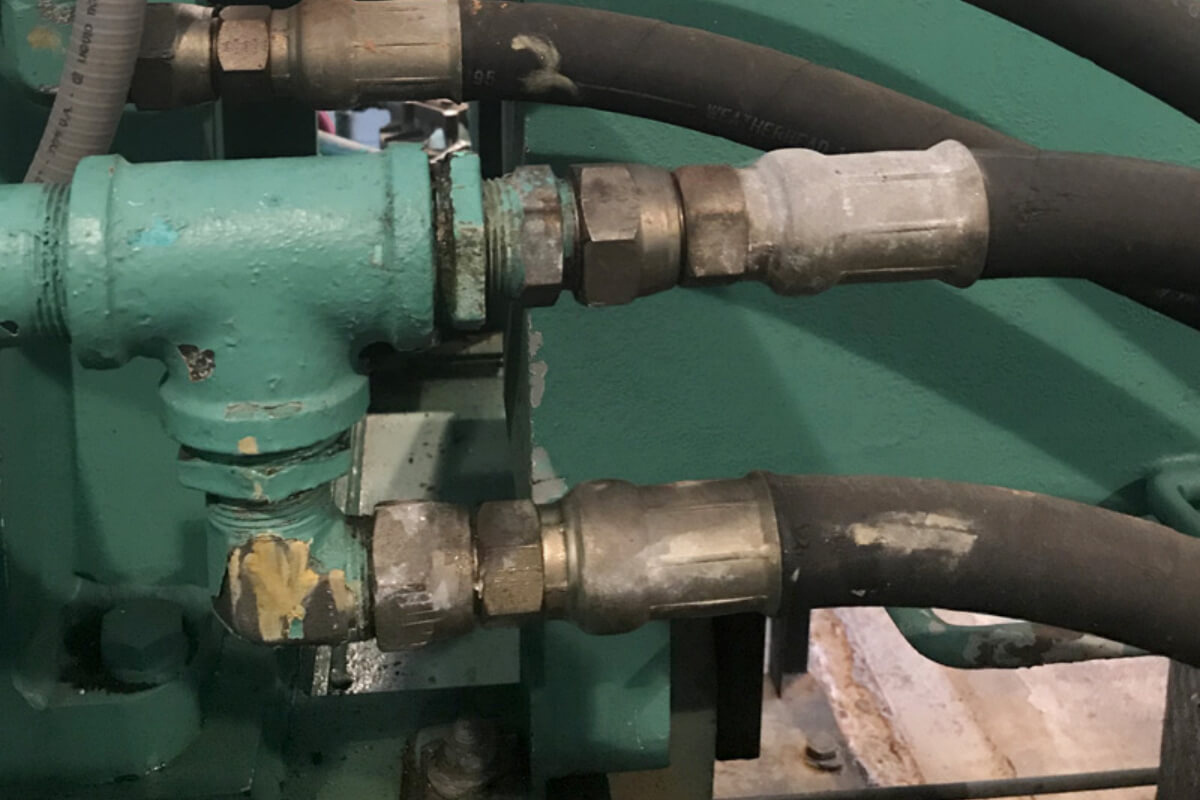
The Solution
Due to the unit’s age, Velasco opted to invest in a new, upgraded gearbox instead of having the existing unit repaired. The new Philadelphia Gear gearbox features:
- The same footprint as the original gearbox so that it fits on the pump’s existing adapter plate, making alignment during final installation much easier. Philadelphia Gear used the original drawings from 1978 to ensure a correct fit.
- A modified housing for easier access to the pump discharge for quicker and hassle-free maintenance.
- An auxiliary lube oil pump that allows for pre-lubrication before starting and protects the gearbox if the oil pressure drops below the set point.
- A standalone electric over air oil cooler closed loop system that automatically turns on a fan when the temperature starts to rise.
- New instrumentation including an oil temperature switch and a low-pressure shutdown switch to control the lube system and protect the gearbox rotating elements from operating under low to no lubrication conditions.
In addition, Philadelphia Gear provided customer support during pump installation, including a system check to set the relief valve and proper pressures.
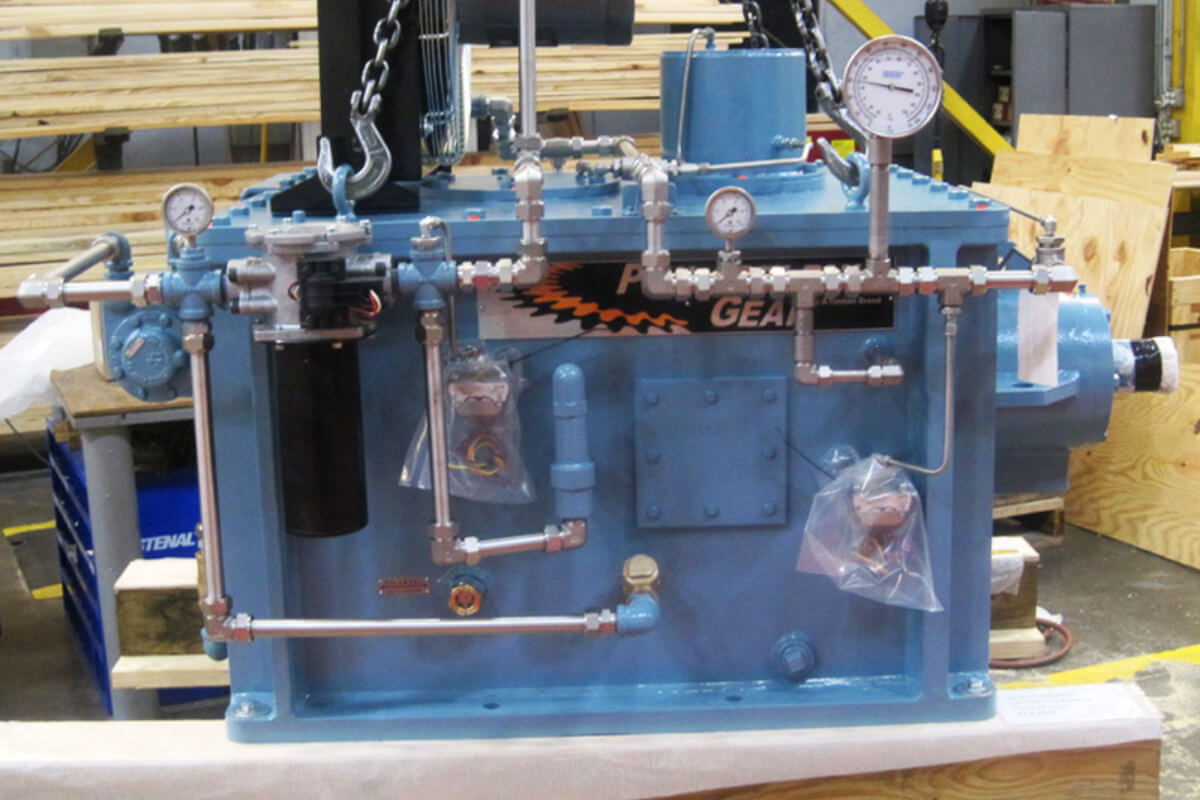
“When failure is not an option, customers call on us for the most reliable gearbox solutions in the industry,” Howard says. “We look forward to helping Velasco with future pump upgrades and expansions that help protect their community.”
Key Results
The new gearbox is expected to operate reliably for 40+ years, minimizing maintenance costs and ensuring that the pump is ready to operate at a moment’s notice.
“We are very satisfied with Philadelphia Gear,” says Joe Williams, general foreman at Velasco Drainage District. “They’ve done a marvelous job of assisting us through this project and many before this, and we are in the process of ordering three more gearboxes.”
Williams also commends Philadelphia Gear for product life and durability, noting that the longest running gearbox in operation at Velasco is currently supporting its Clute-Lake Jackson pump station, where it was installed in 1978.