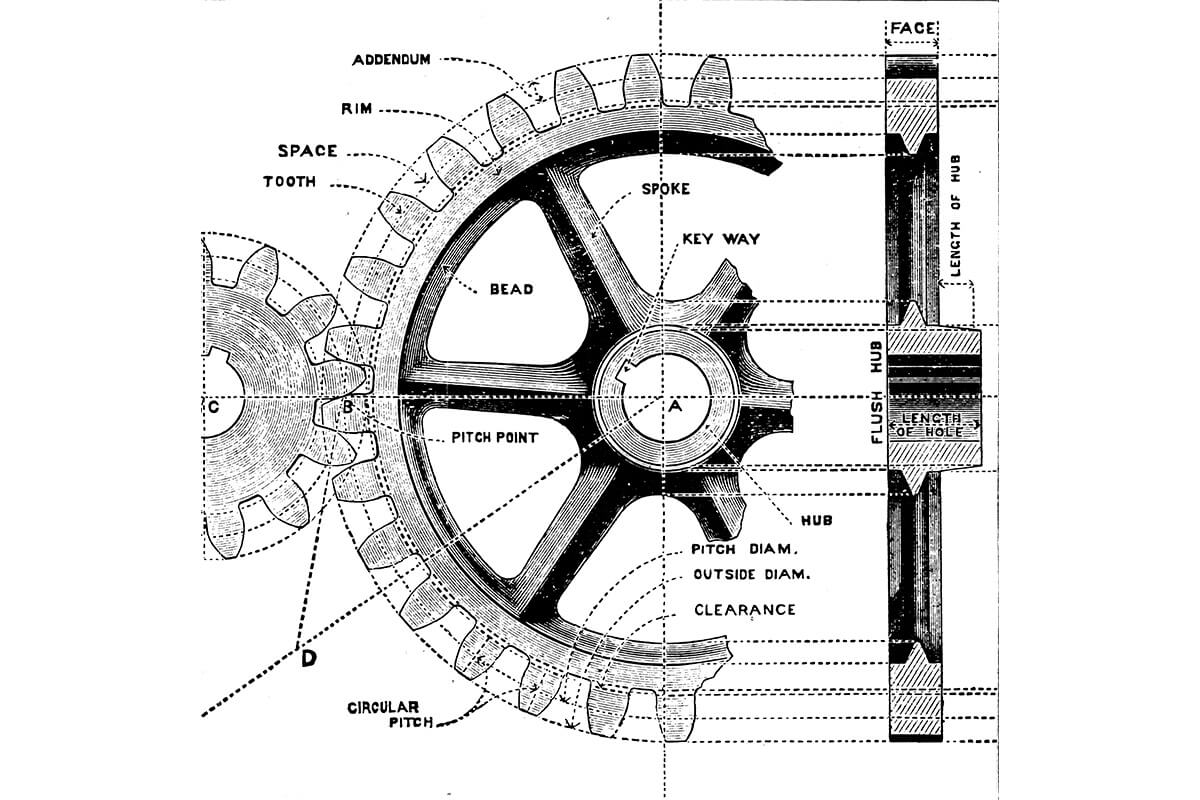
Learn gear fundamentals in four hours
Get your maintenance and operations teams trained with Gear 101: An Introduction to Gearing Concepts and Elemental Gearbox Operation.
Philadelphia Gear’s four-hour program provides a concise yet comprehensive overview of complex rotating equipment — and their foundational operating principles — that keep plants running smoothly.
Go to Gear 101Choosing the Right Gear
Selecting the appropriate gear type depends on factors like load capacity, speed, noise tolerance, space constraints, and environmental conditions. For example, industrial bevel gears excel in high-load, compact setups, while helical gears and double helical gears are preferred for smooth, high-torque applications. Worm gear sets are ideal for high-reduction ratios, and spiral bevel gears offer superior performance in high-speed, heavy-duty systems. Consulting with an experienced manufacturer like Philadelphia Gear® ensures optimal gear selection and reliable performance.
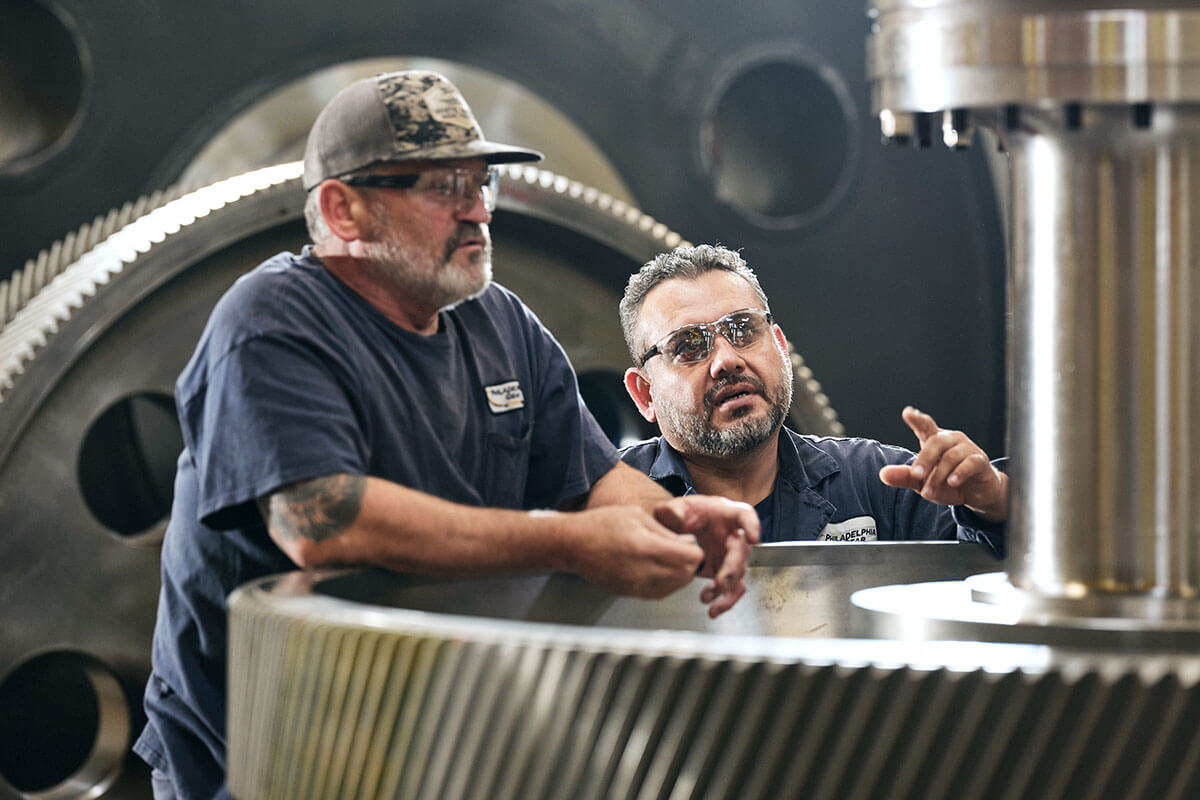
Get the gears you need. Contact Philadelphia Gear today.We’re standing by to help with your most complex gear challenges. Connect with one of our expert specialists today.
Contact us
We’re standing by to help with your most complex gear challenges. Connect with one of our expert specialists today.
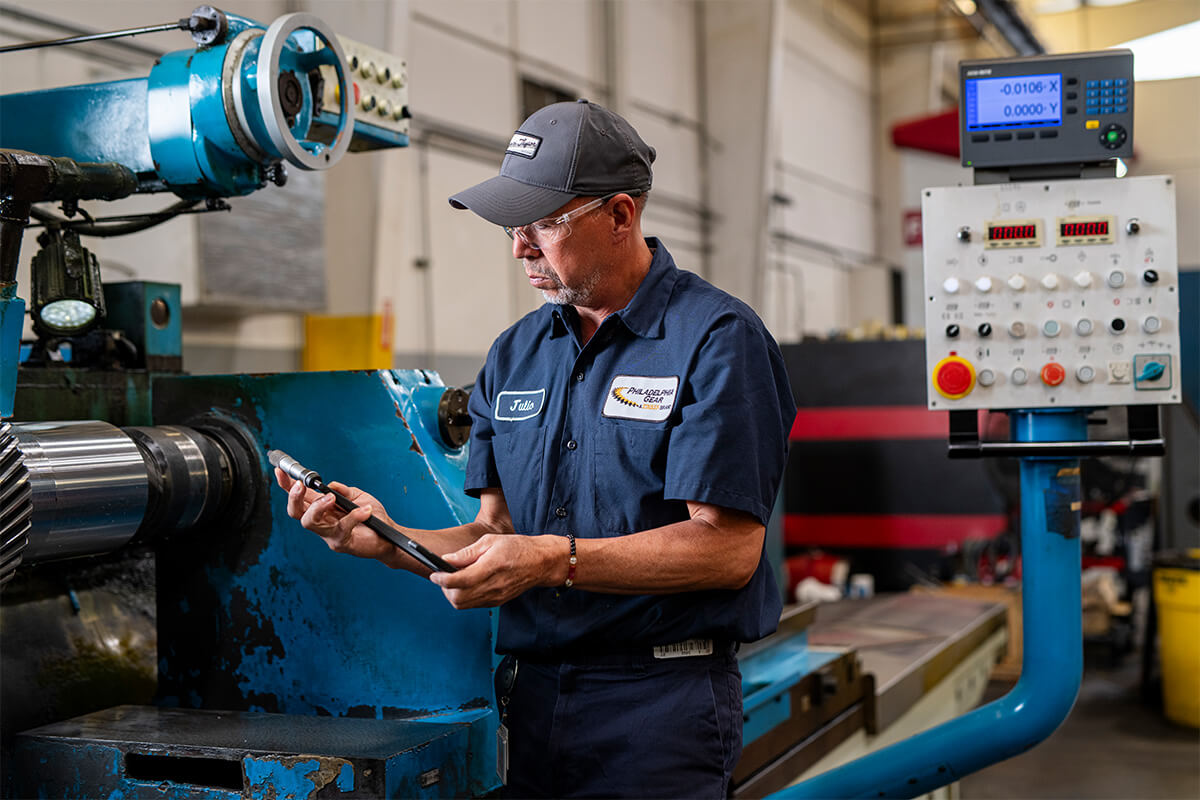