Philadelphia Gear® leverages over 130 years of power transmission engineering expertise to keep critical operations moving. As part of the Timken Power Systems network, our trusted experts and certified facilities support mission-critical industries in the world’s most extreme environments.
RAISING THE BAR FOR QUALITY
Philadelphia Gear’s ultimate goal is delivering 100% TSB: 100% On Time. 100% On Spec. 100% On Budget. As a trusted gear company, our success was built delivering on the TSB promise to our customers and to one another.
Our products adhere to a Quality Management System that is fully compliant with ASQ/ANSI/ISO 9001 standards, providing consistently high levels of service. Each of our regional gear service centers has also been independently audited and ISO-certified, ensuring your mission-critical equipment is in good hands.
For Philadelphia Gear supplier reference, see our Engineering Standards Index.
For more information about our quality process, please contact Quality@PhilaGear.com.
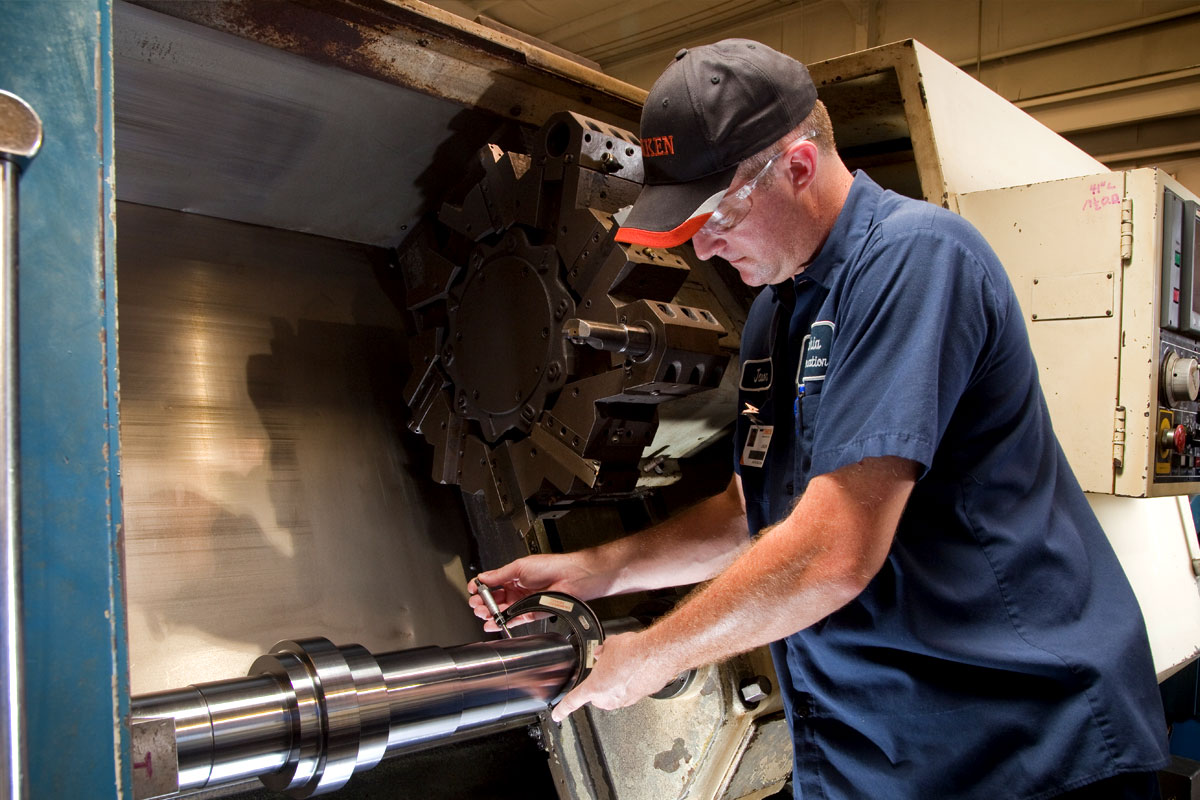
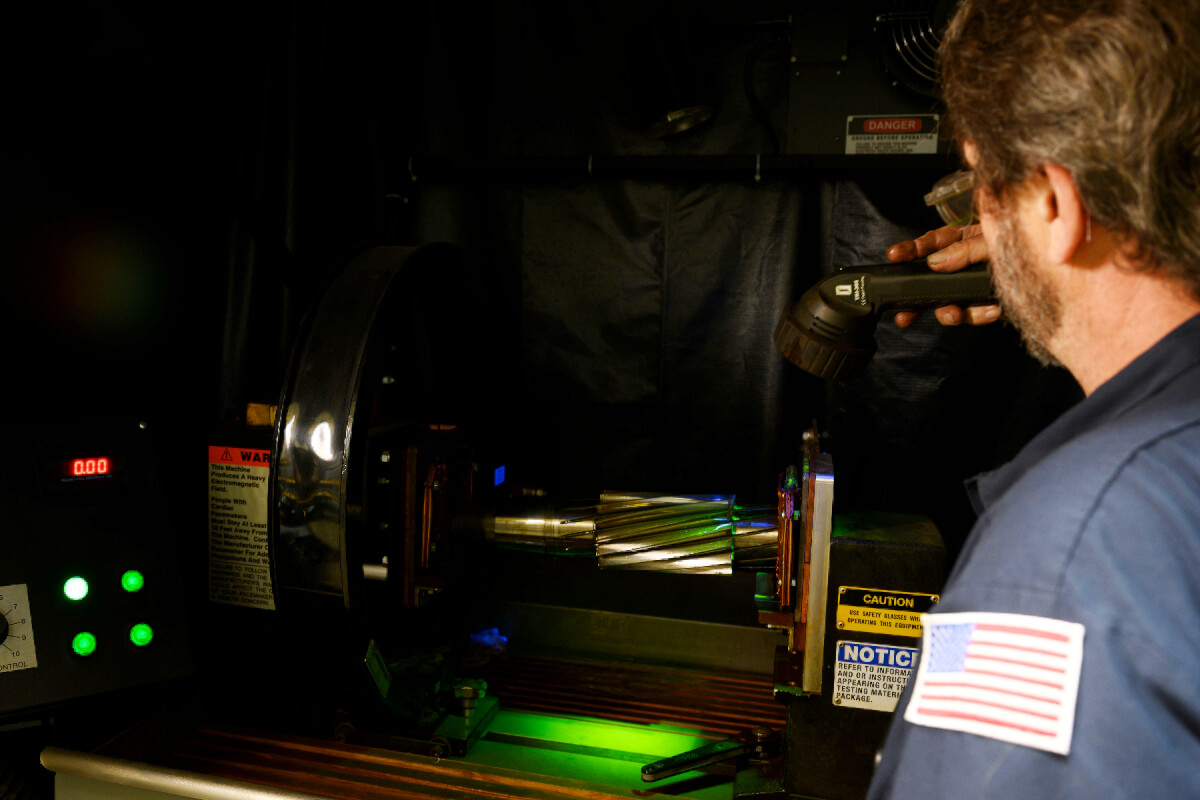
GEARBOX SUPPORT YOU CAN RELY ON
Our best in class 5-Year Standard Warranty comes with every new gearbox to support your most challenging operating environments. In the unlikely event that one of our industrial gearboxes does require service due to defect or workmanship, we’ll repair it fast and cover 100% of our labor and material expense.
And with our best-in-industry 3-Year Service Warranty on regional service center overhauls, you can depend on top-quality performance for years to come.
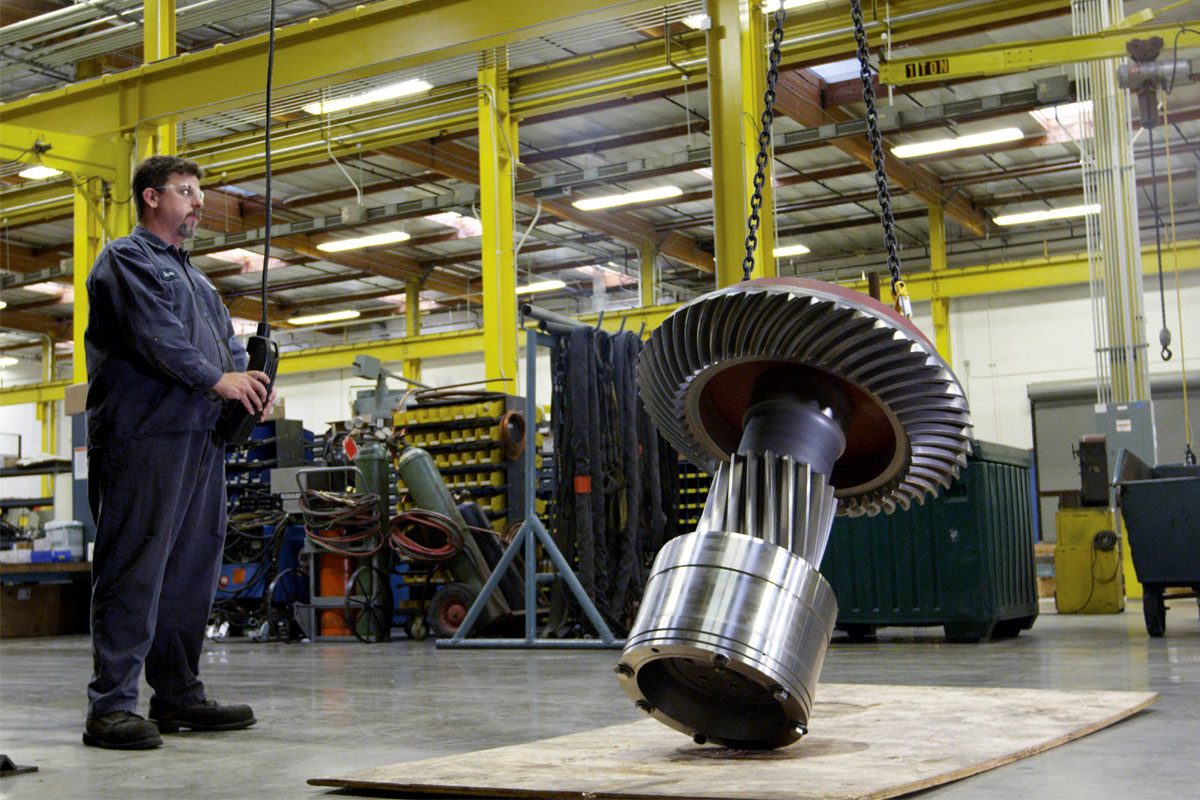
WORK AT PHILADELPHIA GEAR
Our most valuable assets are our people. To continue attracting top talent, Philadelphia Gear and The Timken Company offer competitive pay, benefits, professional development, and continuing education.
SEE OPEN POSITIONS